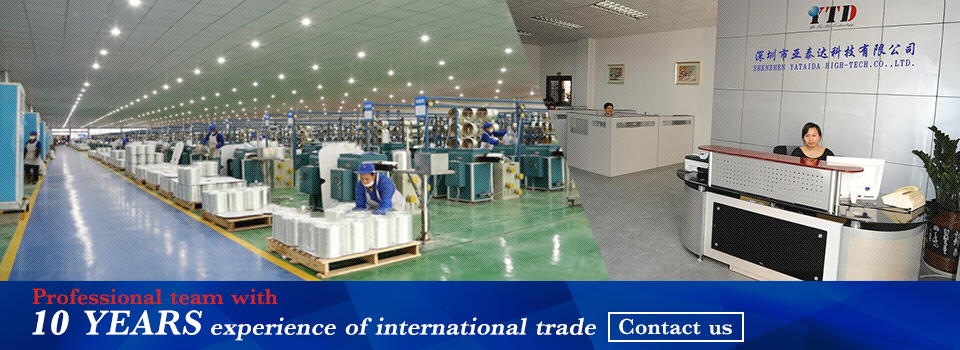
From since the sixties and seventies of the last century, the application of advanced composite materials in civil aircraft from scratch, from less to more, dosage proportion is more and more big, on the Boeing 787 and airbus A350 dosage proportion has reached even more than 50%.Because can bring commercial structure of lightweight composite materials, and improve the reliability, service life and efficiency, thus can assert that the dosage of the composite materials in civil aircraft on proportion will also further expanded.
The present study focuses on
Although the application of composite materials in civil aircraft is becoming more and more widely, but there are also some problems.Composite materials, for example, some big dispersion performance, damage tolerance performance is poor, material shortage, the price is expensive, time-consuming process flow, nondestructive testing and recovery difficulty, lack of comprehensive experimental data and analysis tools, repairs and maintenance of high technical requirements.These problems restrict the further development of composite material, and the innovation of metal materials to composite materials also has brought some challenges.
For civil aircraft, the optimal solution is to find a balance between performance and cost of the plane.Civilian aircraft to both design goal and the goal of the market development, but there will always be a dominant.Obviously, not a lot of r&d spending, it is difficult to achieve a 40% reduction in cost and 30% weight at the same time these two goals.
For this reason, attention should be paid the following research in the field of:
Manufacturing techniques.Improve manufacturing technology is to reduce cost and improve the safety of the key factors.Higher degree of automation, better quality control, less cost and faster recovery cycle, etc., will effectively reduce the manufacturing cost and improve safety.In recent years, automatic wire process, liquid forming process, the autoclave molding process, as well as thermoplastic materials and honeycomb material development and application of automatic manufacturing technology have greatly promoted the composites manufacturing cost is reduced.
Design and analysis tools development and simulation technology.Only on the material and process engineering have enough understanding, to formulate feasible new solutions.Otherwise, a single high safety factor, can make the characteristics of lightweight composite materials, and increase unnecessary costs.Highly integrated design is the development of composite material design and simulation tools, shorten the development cycle, improve the structure performance and reliability of the major challenges.Integrated design need according to the characteristics of material and process, and the basic and cast fiber structure layer, curing characteristics, cementation, and fiber and matrix structure mainly affects the performance of the factors are taken into account.This request will be complex and cast fiber structure layer process, and independent simulation tools such as mold, curing and connection integration as a design tool, design and manufacture to reduce cost, at the same time enhance the structure performance.
superior performance of nanometer materials are used in composite materials, greatly improve the performance of the composite materials.However, the feasibility and cost problem of nanotechnology also restrict the practical application, the material of the basic research and process performance remains to be further research.
Connection design technology.Connection performance boost and its manufacturing process simplification will greatly enhance safety and reduce the cost.Several important research direction in the field include: low temperature bonding technology, advanced solidification technology based on laser or microwave heating, used to repair the debonding technology, automatic assembly technology, etc.
Connection design technology.Connection performance boost and its manufacturing process simplification will greatly enhance safety and reduce the cost.Several important research direction in the field include: low temperature bonding technology, advanced solidification technology based on laser or microwave heating, used to repair the debonding technology, automatic assembly technology, etc.
At present more attention such studies including composite structure damage and fatigue life prediction technology research, composite materials to lightning damage and electromagnetic protection mechanism model research, the efficient of heat-resisting alloy simulation of multi-scale analysis and the damage evolution model for the study of particle modified polymer, etc.In addition, the researchers are working on biomimetic materials and structure and ultrastructure of body of research, and developed the structure plane has the feeling should be self-healing function of new materials and new structure.